Essential Strategies to Future-Proof Your Industrial Control Systems Pt 1
- Emenem Industrial
- May 28, 2024
- 6 min read
Updated: Aug 5, 2024
In today's ever-changing industrial world, it's absolutely crucial to future-proof industrial control systems (ICS). As technology keeps advancing, industries need to adapt and ensure that their systems remain efficient, secure, and resilient. This means not only updating current technologies but also staying ahead of future developments to stay competitive.
Future-proofing ICS requires a well-rounded approach. It involves understanding the evolving landscape of industrial automation, adopting scalable and modular architectures, embracing open standards and interoperability, investing in robust cybersecurity measures, and incorporating predictive maintenance and monitoring. Each of these elements plays a vital role in creating systems that can not only meet the demands of today but also tackle the challenges of tomorrow.
In this comprehensive guide, we delve into the importance of these strategies in detail. We offer insights into how industries can effectively implement them to enhance their operational capabilities and secure their long-term success.
So, let's dive in and explore how you can future-proof your industrial control systems!
Sub-topic discussed
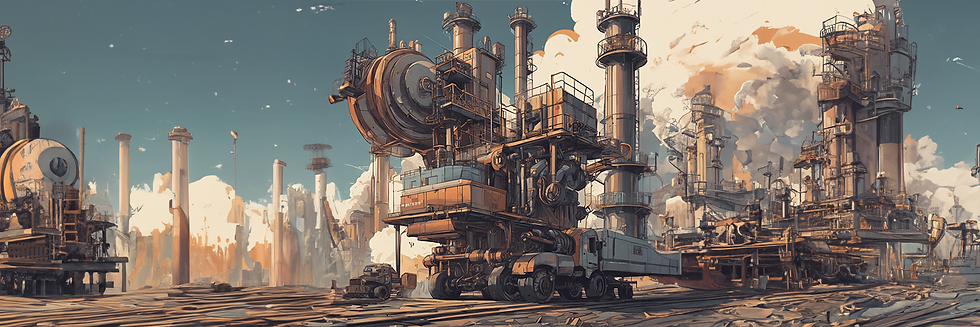
Understanding the Importance of Future-Proofing Industrial Control Systems
The Evolving Landscape of Industrial Automation
Industrial automation has been a vital part of manufacturing and production for many years. With technology constantly advancing, the world of industrial automation is going through some major changes. Let's take a look at some important trends that are shaping this evolution. Here are some key trends shaping this evolution:
Integration of IoT Devices
Enhanced Connectivity: IoT devices enable real-time monitoring and control of industrial processes.
Data Collection: These devices gather vast amounts of data, providing valuable insights for optimizing operations.
Implementation of AI and ML Algorithms
Shirt Towards Smart Manufacturing
Industries in South Africa, just like in many other parts of the world, are jumping on the smart manufacturing bandwagon. A report by the IDC predicts that global spending on IoT in manufacturing will exceed $1 trillion by 2025, showing a strong shift towards digitization and automation.
The goal here is to strike a balance between a casual and informative tone while maintaining the accuracy and integrity of the original information. Let me know if there's anything else I can assist you with!
The Consequences of Outdated Control Systems
Relying on outdated control systems can have several detrimental effects on an organization. These include:
Lack of Integration Capabilities
Data Silos: Older systems often cannot integrate with new technologies, leading to isolated pockets of information.
Inefficient Decision-Making: Limited data sharing hampers comprehensive analysis and informed decision-making.
Increased Vulnerability to Cyber Threats
Maintenance Challenges
A notable example of the consequences of outdated control systems is the case of the WannaCry ransomware attack in 2017. The attack affected numerous organizations worldwide, including major manufacturing facilities. Key points of the incident include:
Exploitation of Vulnerabilities: WannaCry targeted vulnerabilities in outdated Windows operating systems.
Widespread Disruption: The attack caused significant operational disruptions and financial losses.
Understanding the importance of future-proofing industrial control systems is crucial for any organization aiming to thrive in the evolving landscape of industrial automation. Key benefits include:
Enhanced Operational Efficiency: Embracing new technologies improves process efficiency and reduces downtime.
Improved Cybersecurity: Modern systems are better equipped to handle contemporary cyber threats.
Sustained Competitiveness: Staying ahead of technological advancements ensures a competitive edge in the market.
By future-proofing their systems, companies not only enhance their own operations but also contribute to the broader economic development of South Africa, aligning with national goals for industrial growth and innovation.
Implementing Scalable and Modular Architectures
As we dive deeper into our interconnected and tech-savvy world, it's crucial to create control systems that can roll with the punches and adapt to evolving needs. One way to future-proof industrial control systems is by using scalable and modular architectures.
The goal here is to strike a balance between being informative and casual while staying true to the original content. Let me know if there's anything specific you'd like me to focus on or if you have any preferences for the tone of voice.
Benefits of Scalable Systems
Scalable systems offer numerous advantages that contribute to both immediate and long-term operational success:
Flexibility to Grow Demand
Easily Expandable: Scalable systems allow for seamless addition of new components or capabilities without overhauling the entire system.
Adaptability: As production demands increase, scalable systems can be adjusted to handle greater workloads, ensuring consistent performance.
Cost Efficiency
Enhanced Performace and Reliability
Examples of Modular Design in Industrial Control Systems
Modular design is a core principle of scalable architectures, providing the building blocks for flexible and efficient industrial control systems. Here are some examples of how modular design is applied:
Distributed Control Systems (DCS)
Modular Controllers: DCS architectures often use modular controllers that can be added or removed as needed, facilitating easy upgrades and maintenance.
Networked Components: Components such as sensors, actuators, and controllers are networked, allowing for scalable and flexible system configuration.
Programmable Logic Controllers (PLC)
Industrial Internet of Things (IIoT) Platforms
Modular Machine Design
Implementing scalable and modular architectures is super important for future-proofing industrial control systems. You see, scalability brings a bunch of benefits like flexibility, cost efficiency, and better performance, which are all super crucial in today's rapidly changing industrial landscape. Let me give you some examples of how modular design is applied in real-life scenarios, from Distributed Control Systems to Industrial IoT platforms. These examples show how these principles are put into practice, making sure that systems can easily adapt to new technologies and increasing demands.
By adopting scalable and modular architectures, organizations can make sure that their industrial control systems stay strong, flexible, and ready to tackle future challenges. This smart approach not only improves operational efficiency but also boosts competitiveness and sparks innovation in the industrial sector.
So, the idea behind this combination of system and user prompts is to optimize the assistant's ability to make the text sound more like it was written by a human while keeping the original intent and making sure all the facts are accurate.
Embracing Open Standards and Interoperability
Building on the principles of scalability and modularity, embracing open standards and ensuring interoperability are critical steps in future-proofing industrial control systems. Open standards and interoperability enable diverse systems and components to communicate and work together seamlessly, fostering innovation and efficiency.
Advantages of Open Standards
Adopting open standards offers several significant benefits:
Enhanced Compatibility
Seamless Integration: Open standards facilitate the integration of different systems and components, regardless of the manufacturer, reducing compatibility issues.
Vendor Neutrality: Companies are not locked into a single vendor, allowing for more flexibility in choosing the best components and solutions.
Cost Savings
Innovation and Flexibility
Improved Security
Key Interoperability Protocols and Standards
Several key interoperability protocols and standards play a crucial role in industrial control systems:
OPC UA (Open Platform Communications Unified Architecture)
Unified Framework: OPC UA provides a unified framework for secure and reliable data exchange between devices and systems in industrial automation.
Scalability and Flexibility: It supports complex information models and can be scaled from small devices to enterprise systems.
Platform Independence: OPC UA is platform-independent, ensuring compatibility across different operating systems and hardware.
MQTT (Message Queuing Telemetry Transport)
PROFINET
EtherCAT (Ethernet for Control Automation Technology)
Using open rules and making sure things work well together are key for keeping factory control systems up-to-date. The plus points of open rules—like better working together, less cost, new ideas, choice, and better safety—show why they're big in today's factory world. The main ways for things to talk well, like OPC UA, MQTT, PROFINET, and EtherCAT, give the right plans for smooth chat and mix of many systems and parts.
By picking open rules and putting working first, groups can make strong, bendy, and ready-for-the-future factory control systems. This way, they don't just make work run better, but also make sure systems can change with new tech and work ways, keeping ahead in the fast-change factory scene.
Investing in Cybersecurity
In the world of factory control systems, having strong cyber safety steps is very key. As we use open rules and build out designs more, making sure these systems are safe from web risks is a top need.
Common Cybersecurity Threats in Industrial Environments
Industrial environments face a range of cybersecurity threats that can disrupt operations, compromise data integrity, and even endanger safety. Key threats include:
Malware and Ransomware
Malware: Malicious software designed to infiltrate and damage systems, often causing operational disruptions.
Ransomware: A type of malware that encrypts data and demands a ransom for its release. The 2017 WannaCry attack is a notable example, affecting numerous industrial systems worldwide.
Phishing and Social Engineering
Advanced Persistent Threats
Insider Treats
Denial-of-Service (DoS) Attacks
Best Practices for Securing Industrial Control Systems
To protect industrial control systems from these threats, it is essential to implement comprehensive cybersecurity measures. Best practices include:
Networks Segmentation
Isolated Networks: Segregate critical control networks from corporate IT networks and the internet to limit exposure.
Zoning and Conduits: Implement zones of trust with controlled conduits between them, ensuring that only authorized traffic can pass.
Regular Updates and Patch Management
Strong Access Controls
Continuous Monitoring and Incident Response
Employee Training and Awareness
Backup and Recovery
Security Audits and Assessments
Putting money into cyber safe-keeping is key to keep industry control gear safe from lots of dangers. By knowing the usual web threats like bad software, scam emails, advanced threats from pros, risks from within, and overload attacks, groups can get ready and guard their stuff better. Using good steps, like cutting the network into parts, always updating, strong limits on who can get in, watching all the time, teaching workers, and having strong save plans, makes sure a well-covered fight against cyber dangers.
By putting cyber safe-keeping first, industry groups can keep their work and info safe, and also make their whole system more sure and strong. This get-ahead way is so needed to keep a safe, work-well, and ready-for-tomorrow industry place.
Incorporating Predictive Maintenance and Monitoring
As industrial control systems become more advanced, incorporating predictive maintenance and effective monitoring is essential to enhance the operational efficiency and longevity of equipment. This approach helps in reducing downtime and ensuring the smooth functioning of industrial processes.
How Predictive Maintenance Reduces Downtime and Extends Equipment Life
Predictive maintenance leverages data and advanced analytics to predict when equipment failures might occur, allowing for proactive maintenance. The benefits are substantial:
Minimized Downtime
Early Detection of Issues: By continuously monitoring equipment performance, predictive maintenance can identify potential problems before they lead to failures, reducing unplanned downtime.
Scheduled Maintenance: Maintenance activities can be scheduled during planned downtimes or off-peak hours, minimizing disruption to production.
Extended Equipment Life
Cost Savings
Enhanced Safety and Compliance
Tools and Technologies for Effective Monitoring
To implement predictive maintenance effectively, several tools and technologies are essential. These include:
Sensors and IoT Devices
Real-Time Data Collection: Sensors and IoT devices collect real-time data on various parameters such as temperature, vibration, pressure, and more.
Wireless Communication: These devices often use wireless communication protocols to transmit data to central monitoring systems.
Condition monitoring Systems
Data Analytics and Machine Learning
Cloud-Based Platforms
Digital Twins
Mobile and Remote Monitoring
Using smart care and a good watch is key to keeping machines and control systems working well and for a long time. Smart care cuts down on stop time and makes gear last longer by spotting problems early, setting the best times to fix things, and stopping big breaks. Using top tools and techs, like feelers, web-connected things, number study, cloud spaces, twin models, and phone watches is key in making these plans work well.
By picking smart care and watch, places can save a lot of money, make things safer, and match with what the work world says must be done. This forward-looking way not only makes work run smoother but also helps the whole making-things world stay strong and in the game.
In summary
Future-proofing industrial control systems is essential for any organization aiming to thrive in the modern industrial era. By understanding the evolving landscape of industrial automation, organizations can appreciate the critical need for updating their control systems. Implementing scalable and modular architectures provides the flexibility to grow and adapt to changing demands, ensuring cost efficiency and optimal performance.
Embracing open standards and interoperability further enhances system compatibility and innovation, allowing diverse components to work seamlessly together. Meanwhile, investing in cybersecurity protects these advanced systems from a myriad of threats, safeguarding data integrity and operational continuity.
Lastly, incorporating predictive maintenance and monitoring leverages data and advanced analytics to reduce downtime and extend the life of equipment, leading to significant cost savings and improved operational efficiency.
By integrating these strategies, industries can build robust, adaptable, and secure control systems, ensuring they remain competitive and resilient in the face of future technological advancements and challenges. This holistic approach not only optimizes current operations but also positions organizations for sustained success in the dynamic industrial landscape.
Need help with your maintenance management? Visit our website [Emenem Industrial] or contact us.
References
IDC. (2020). Global IoT Spending Guide. Retrieved from IDC website.
IBM Security. (2020). Cost of a Data Breach Report 2020. Retrieved from IBM website.
BBC News. (2017). WannaCry ransomware: Everything you need to know. Retrieved from BBC News.
Siemens. (2021). Benefits of Scalable Automation Systems. Retrieved from Siemens website.
Rockwell Automation. (2020). Modular Automation Systems. Retrieved from Rockwell Automation website.
McKinsey & Company. (2021). The Industrial IoT Imperative. Retrieved from McKinsey website.
OPC Foundation. (2021). What is OPC UA? Retrieved from OPC Foundation website.
MQTT.org. (2020). MQTT: The Standard for IoT Messaging. Retrieved from MQTT.org website.
Siemens. (2021). PROFINET: The Standard for Industrial Networking. Retrieved from Siemens website.
EtherCAT Technology Group. (2021). EtherCAT – Industrial Ethernet for Real-Time Automation. Retrieved from EtherCAT website.
Cybersecurity & Infrastructure Security Agency (CISA). (2021). Industrial Control Systems Cybersecurity. Retrieved from CISA website.
IBM Security. (2021). X-Force Threat Intelligence Index. Retrieved from IBM website.
Symantec. (2020). The Impact of Ransomware on Industrial Control Systems. Retrieved from Symantec website.
McKinsey & Company. (2020). The Future of Predictive Maintenance. Retrieved from McKinsey website.
General Electric. (2021). Predictive Maintenance for Industrial Equipment. Retrieved from GE website.
IBM. (2020). Predictive Maintenance: Using AI and IoT to Reduce Downtime. Retrieved from IBM website.
Comments